На механические свойства порошкового покрытия влияет не только качество ЛКМ, но и правильная подготовка окрашиваемой поверхности, способ нанесения краски и соблюдение предписанных производителем технологических режимов полимеризации.

Для того, чтобы в будущем не тратить ресурсы на устранение дефектов, необходимо уделять должное внимание подготовке поверхности перед порошковой покраской. Декоративные свойства и длительность эксплуатации изделия напрямую зависят от качества подготовки поверхности перед окраской.
Основная цель подготовки поверхности - удаление веществ, которые препятствуют окрашиванию и ускоряют коррозионные процессы, а также получение поверхности, которая обеспечивает необходимую адгезию металлической подложки с лакокрасочным покрытием.
Подготовка поверхности перед порошковым напылением состоит нескольких этапов.
Этап 1 Очистка от загрязнений
Существует три метода очистки:
- Механическая;
- Химическая
- Термическая
Подготовка поверхности механическими методами включает в себя: абразивную обработку (пескоструйная, гидропескоструйная, дробеструйная и др.), шлифование, полирование, крацевание и т.п. Механический метод подготовки используют при окрашивании крупногабаритных металлоконструкций в строительстве, нефте- и газодобывающей промышленности, судостроении и судоремонте, энергетике, городском хозяйстве и т. д.
Химическая очистка осуществляется с использованием щелочных, кислотных или нейтральных веществ, а также растворителей. Вещество подбирается в зависимости от вида и степени загрязнения, типа, материала и размера обрабатываемой поверхности. Химический метод очистки используют на предприятиях автомобилестроения, машиностроения, приборостроения, производства бытовой техники.
Термический метод. Поверхность под окраску обрабатывают пламенем кислородно-ацетиленовой горелки (при избытке кислорода до 30%). Достоинства термической очистки - обезжиривание поверхности одновременное с очисткой от окалины и ржавчины. Данный метод используют редко в случаях перекраски изделий, совместно с механическим способом.
- Исходное состояние поверхности
- Условия эксплуатации изделия
- Материал и характеристики изделия.
Этап 2. Обезжиривание.
Обезжиривание необходимо для того, чтобы удалить маслянистые и жировые загрязнения с поверхности. В процессе обезжиривания применяют специальные растворители: керосин, уай-спирит, трихлорэтилен, бензин, растворы различных солей и щелочей. Изделие погружают в ванну с растворителем, омывают им или просто протирают поверхность металла. Обезжиривание подразделяется на: химическое и электрохимическое, ультразвуковое, термическое.
Этап 3. Химическая подготовка поверхности.
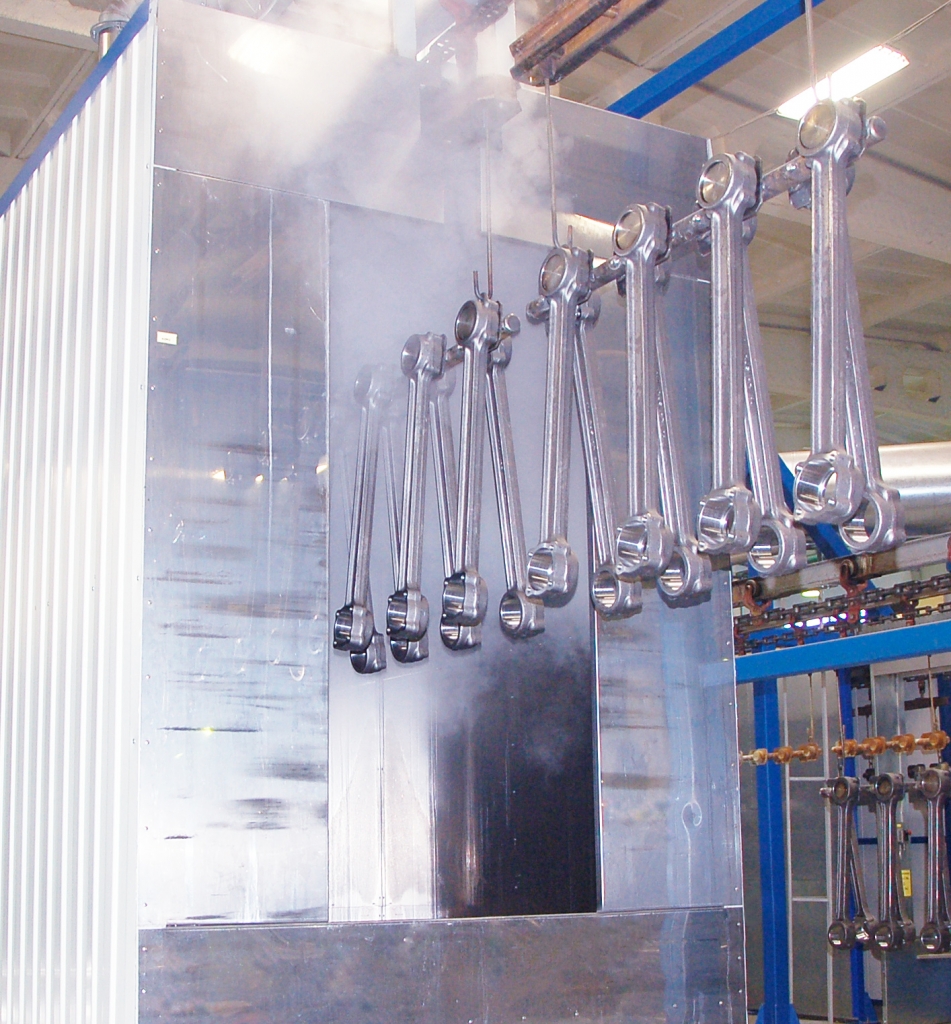
Для того, чтобы придать покрытию дополнительную коррозионную стойкость, после очистки и обезжиривания проводят специальную химическую подготовку поверхности: фосфатирование, хроматирование, пассивирование.
Химическая обработка способствует улучшению адгезии («сцепляемости») порошковой краски с поверхностью металла и повышает антикоррозийные свойства покрытия. Обычно поверхность обрабатывается фосфатом железа (для стальных поверхностей), цинка (для гальванических элементов), хрома (для алюминиевых материалов) или марганца, а также хромового ангидрида. Для алюминия и его сплавов часто применяют методы хроматирования или анодирования.
Подготовку металлических изделий перед нанесением порошковой краски осуществляют в соответствии с ГОСТ 9.402. Согласно ГОСТ 9.402, предназначенные для окраски поверхности должны быть сухими, обезжиренными, без следов коррозии и других загрязнений.
Окраска изделий порошковыми красками происходит методом электростатического напыления.
Метод представляет собой нанесение на заземленное изделие электростатически заряженной порошковой краски с помощью пневматического распылителя. Специалисты по порошковой окраске называют распылитель также пульверизатором, пистолетом или аппликатором.
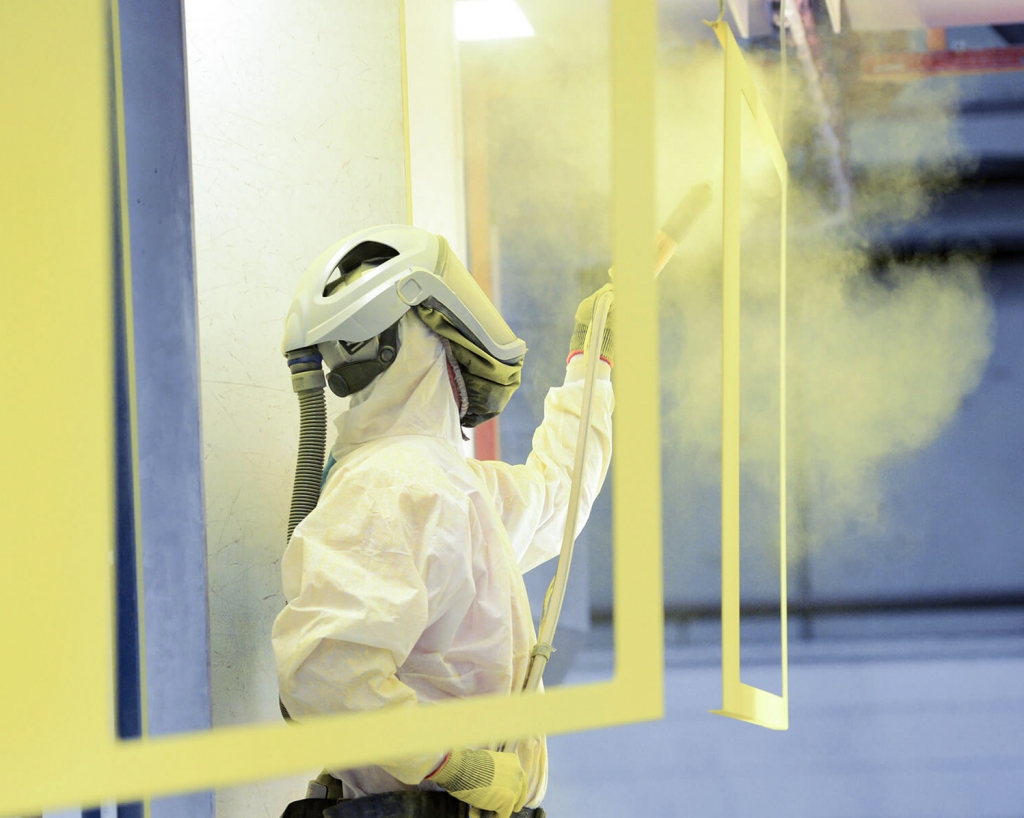
Как происходит напыление.
Сначала маляр засыпает порошковую краску в питатель. При включении пистолета, сжатый воздух подается под давлением через питатель и переводит порошок во взвешенное состояние, образовывая так называемый «кипящий слой» краски.
Далее воздушный насос (эжектор), забирает аэровзвесь из контейнера, разбавляет ее воздухом до более низкой концентрации и подает в напылитель, где порошковая краска приобретает электростатический заряд. С помощью сжатого воздуха заряженная порошковая краска попадает на заземленную поверхность, оседает и удерживается на ней за счет электростатического притяжения.
Существует две разновидности электростатического распыления:
- Электростатическое с зарядкой частиц в поле коронарного заряда;
- Трибостатическое напыление;
При электростатическом напылении, частицы получают заряд от внешнего источника электроэнергии (коронирующего электрода), а при трибостатическом - в результате их трения о стенки турбины напылителя.
При первом способе коронный заряд поддерживается источником высокого напряжения, встроенным в распылитель. У метода электростатического нанесения есть недостаток. Часто возникают затруднения с нанесением краски на поверхности с глухими отверстиями и углублениями. Это связано с тем, что частицы краски осаждаются сначала на выступающих участках поверхности и как следствие, она может быть прокрашена неравномерно.
Для окрашивания сложных изделий и деталей, чаще всего используют трибостатическое напыление. Сжатый воздух распыляет краску, а заряд, приобретенный в результате трения о диэлектрик, удерживает ее на поверхности. В качестве диэлектрика используется фторопласт, из которого изготовлены отдельные части краскораспылителя. Трибостатический способ применяют для окрашивания деталей, имеющих сложную форму.
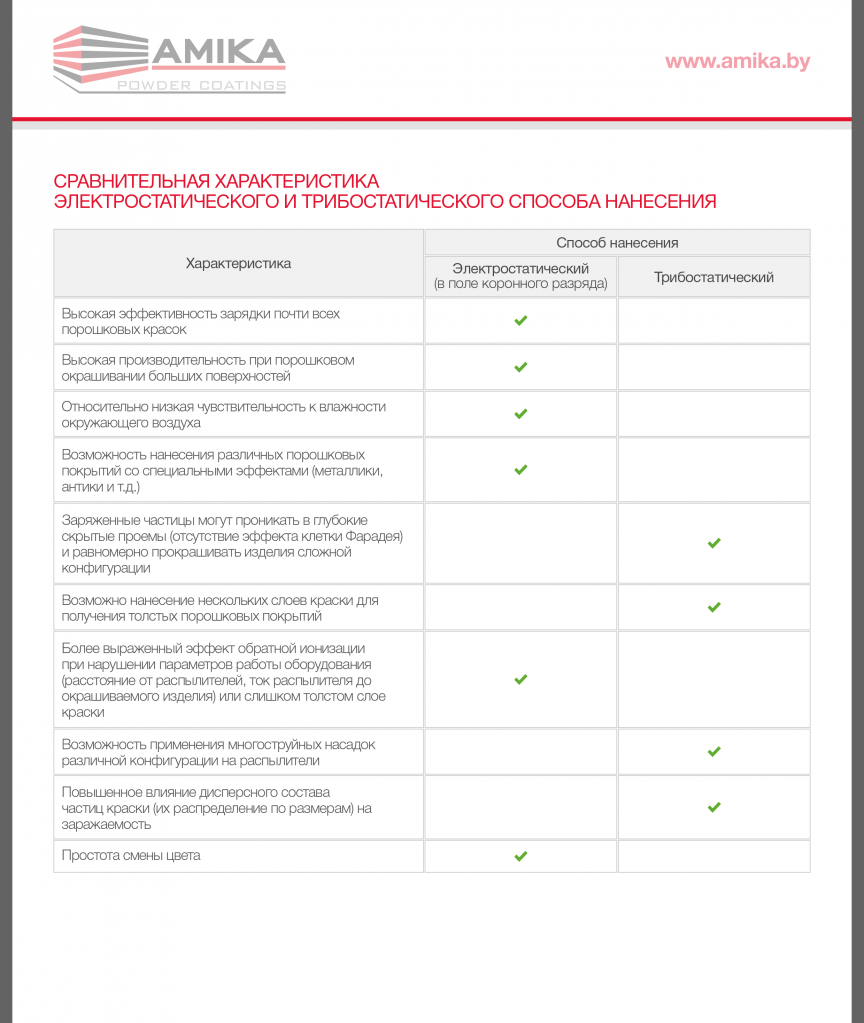
СРАВНИТЕЛЬНАЯ ХАРАКТЕРИСТИКА
ЭЛЕКТРОСТАТИЧЕСКОГО И ТРИБОСТАТИЧЕСКОГО СПОСОБА НАНЕСЕНИЯ
Скачать файл PDF
Одно из преимуществ порошковой краски над традиционными ЛКМ – экономия за счет вторичного использования материала (рекуперации), не попавшего на изделие.
Подберите подходящую систему сбора порошковой краски в камере напыления и потеря полимерного материала составит 7%!
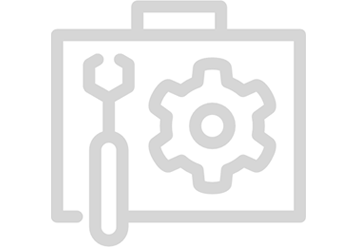
ОПТИМИЗИРУЙТЕ СВОЕ ПРОИЗВОДСТВО:
регулярно проводите технический аудит участка порошковой окраски и будьте уверены, что оборудование настроено правильно!
Честная техническая поддержка AMIKA
Для напыления порошковых красок используют как стационарные установки для ручного напыления, так и автоматические линии окрашивания.
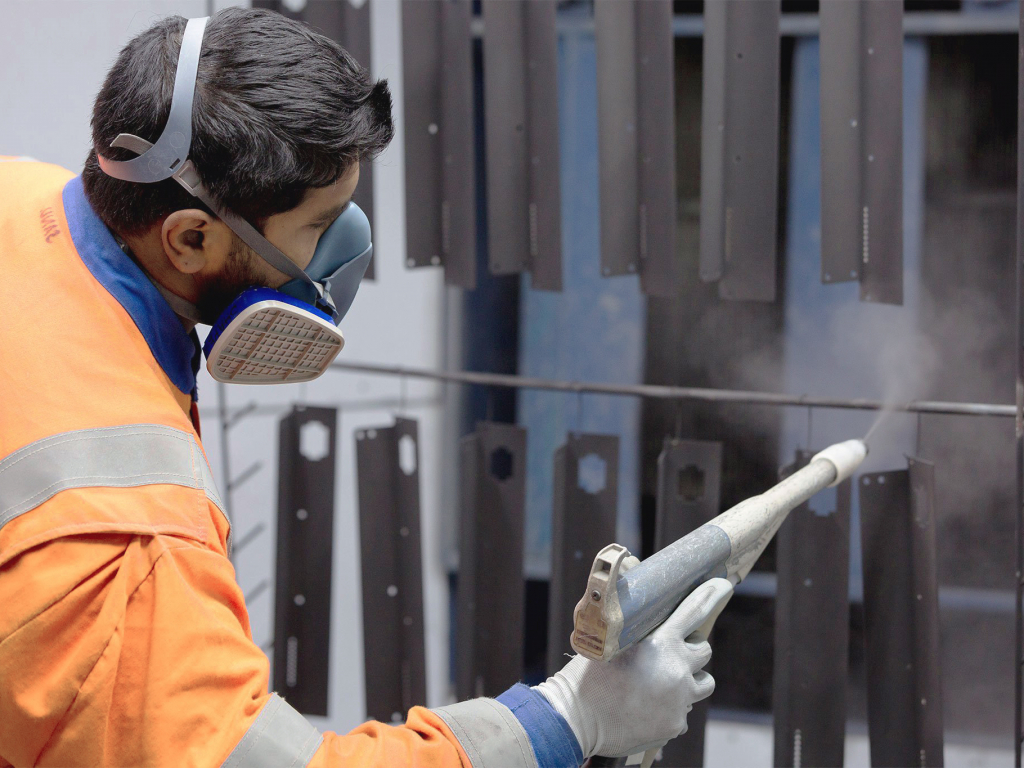
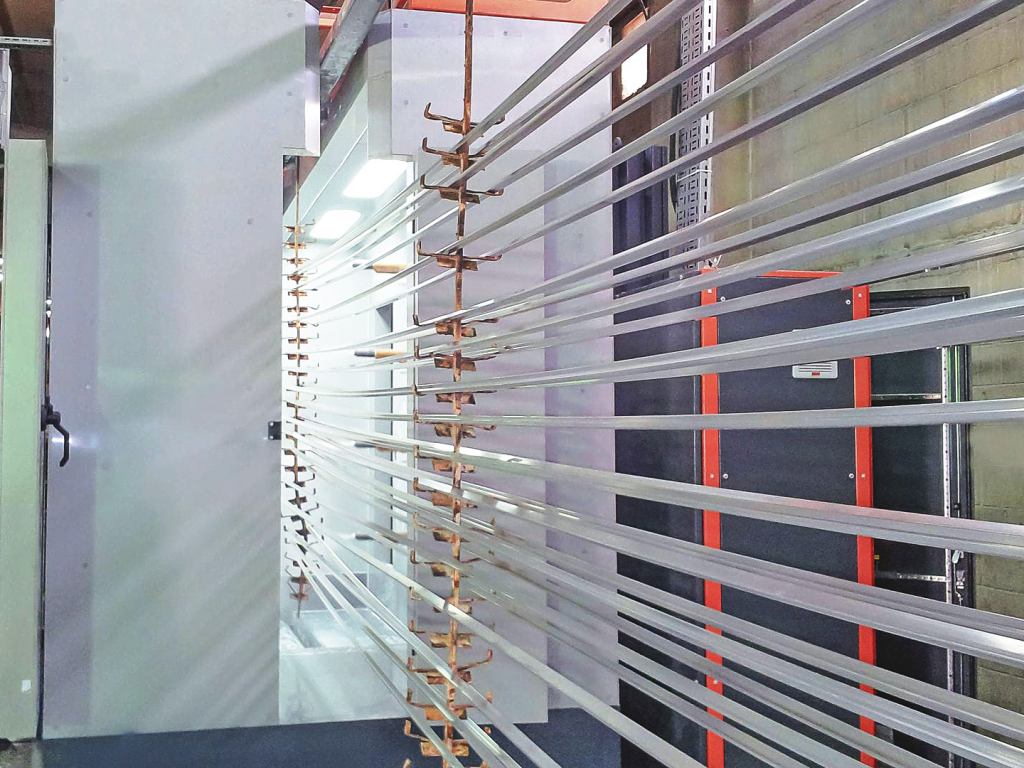
Реакция полимеризации порошковых покрытий происходит при определенной температуре и времени в печи полимеризации. Как правило, горячую сушку порошковых покрытий проводят в диапазоне 150 — 250°C в течении 15 — 30 мин.
Такие условия необходимы для процесса оплавления и образование пленки (полимеризация). Соответствующий режим для формирования покрытия подбираем с учетом вида порошковой краски, материала и толщины стенок окрашиваемого изделия, типа печи и т. д.
Оборудование для полимеризации
Существуют два вида печей полимеризации: камерные и непрерывного действия. Также их называют тупиковыми или проходными печами.
Камерные печи формирования покрытия - самые простые по конструкции печи. Изделия в печь загружают в периодическом режиме.
Этот вид печей используют в двух случаях:
- Небольшие объемы производства
- Постоянно изменяющиеся условия полимеризации: разное время сушки для изделий различной толщины и/или разная температура сушки при использовании разных порошковых материалов.
У тупиковых печей есть недостаток. Из-за того, что загрузка изделий осуществляется партиями и двери сушилки постоянно открываются, температура в печи постоянно изменяется. Чтобы покрытие было равномерным, и прочным необходимо следить за конвекцией воздуха и выделять дополнительное время на прогрев печи после каждой партии.
Содержание масла не более 0,01 мг/м3, содержание влаги – не более 1,3 г/м3, точка росы не выше 7 °С, содержание пыли не более 1 мг/м3.
Для того, чтобы очистить воздух от масла, влаги и пыли, необходимо пропустить его через каскад пылемаслоуловителей и аппарат воздухоосушителя.
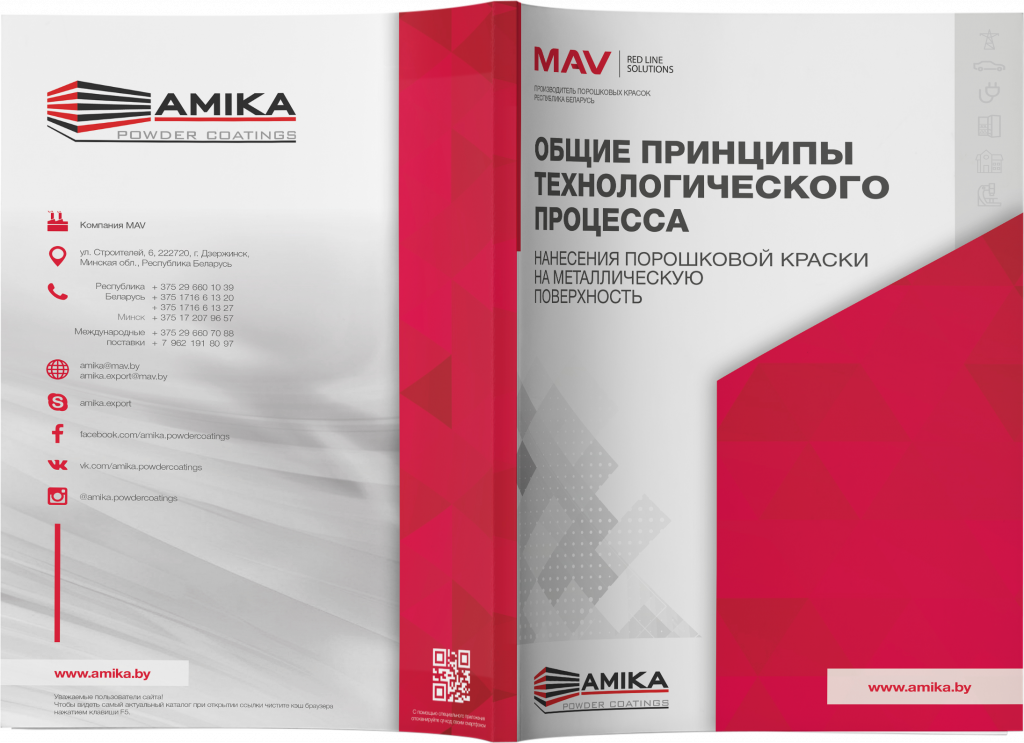
СКАЧИВАЙТЕ "ОБЩИЕ ПРИНЦИПЫ ТЕХНОЛОГИЧЕСКОГО ПРОЦЕССА НАНЕСЕНИЯ ПОРОШКОВОЙ КРАСКИ НА МЕТАЛЛИЧЕСКУЮ ПОВЕРХНОСТЬ"
Скачать файл PDF