- 20 апреля 2020
- AMIKA советует
34 года совместного опыта технической поддержки AMIKA показывает, что Потребители начинают экспериментировать с толщиной стандартных архитектурных и индустриальных порошковых покрытий в двух случаях:
- В погоне за улучшением показателей производительности и экономии;
- В стремлении сделать изделие более прочным и/или атмосферостойким.
ЧЕМ ОПАСНЫ В ТАКИХ СЛУЧАЯХ ТОНКОЕ И ЧРЕЗМЕРНОЕ ТОЛСТОЕ ПОРОШКОВОЕ ПОКРЫТИЕ?
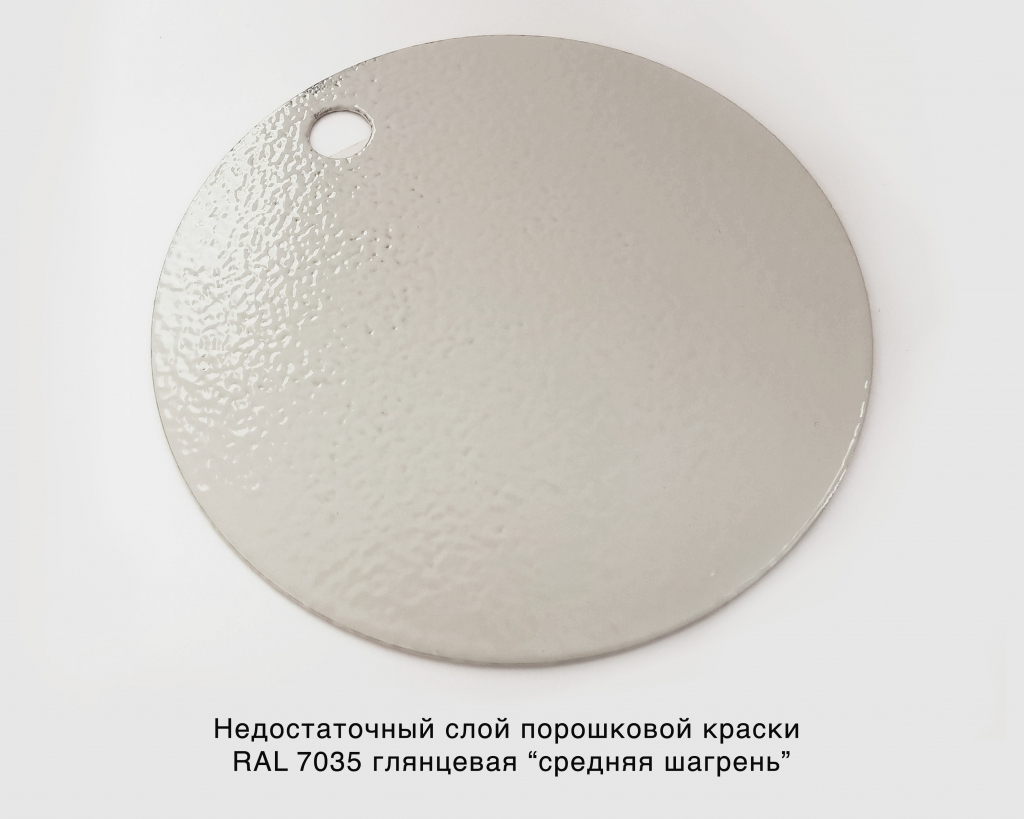
- Просвечивает металлическое основание, покрытие имеет неравномерную структуру и цвет;
- Снижается стойкость покрытия к атмосферным воздействиям;
- Повышается риск появления коррозии;
- Появляются дефекты покрытия - проколы, кратеры, “псевдошагрень” или “апельсиновая корка”;
- Не раскрывается рисунок у структурных покрытий.
- искажает цвет и степень глянца покрытия;
- провоцирует “апельсиновую корку”, отслаивание, подтеки, “эффект рамки”, осыпание полимерного слоя.
- не позволяет порошковому покрытию пройти полный цикл полимеризации. Как следствие - ухудшение адгезии и потеря физико-механических свойств порошково-полимерного покрытия.
К тому же, излишняя толщина полимерного покрытия влечет бОльший расход материала и дополнительные затраты.
Как рассчитать расход краски на м2?
ЧТО ВЛИЯЕТ НА ФОРМИРОВАНИЕ ПОЛИМЕРНОГО ПОКРЫТИЯ И ЕГО ТОЛЩИНУ
1. Назначение лакокрасочного покрытия.
Еще на стадии разработки изделия, в конструкторской документации проектировщик/дизайнер/инженер указывает назначение и класс лакокрасочного покрытия.
Для покрытий декоративного назначения (предметы интерьера, канцелярские товары, корзинки и другие товары народного потребления) приемлема толщина до 60 мкм.
Для защитно–декоративных покрытий (металлические двери, фасадные кассеты, мебель, ограждения, доборные элементы кровли и т.д.) оптимальная толщина покрытия составляет 60–120 мкм, для покрытий со спец.эффектами - до 200 мкм.
Для защитных покрытий (корпуса и детали сельскохозяйственной техники) толщина должна быть в пределах 60–120 мкм, но в особых случаях может быть увеличена до 400–500 мкм.
2. Тип формируемой поверхности.
Производители порошковых ЛКМ в технической документации всегда указывают рекомендованные толщины для каждого вида пленкообразователя и структуры поверхности.
Только при соблюдении данных рекомендаций, производитель может гарантировать соответствие заявленным в технической документации физико-механическим свойствам.
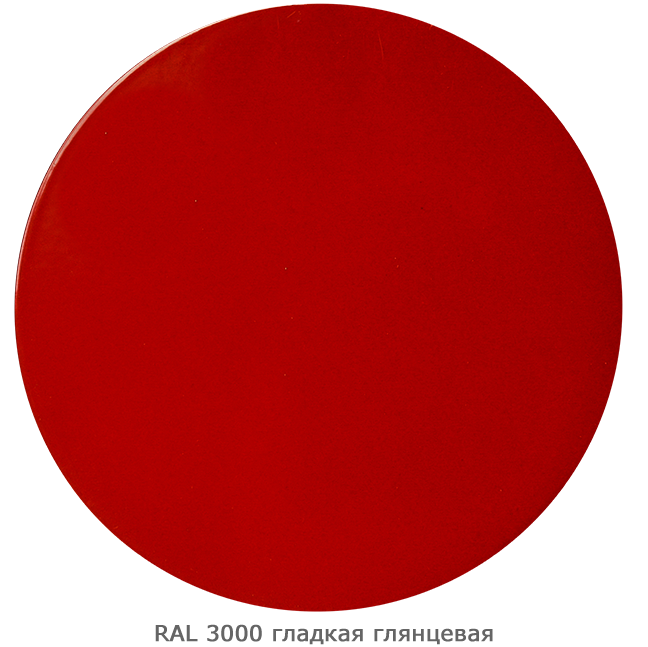
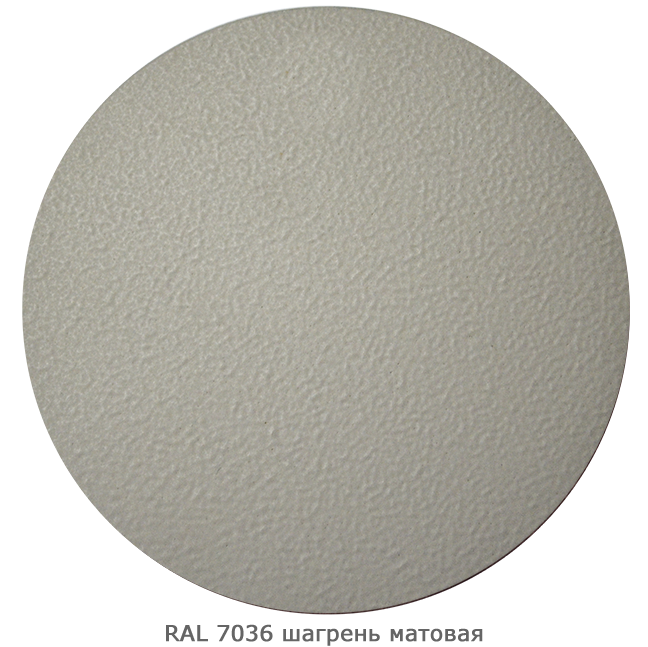
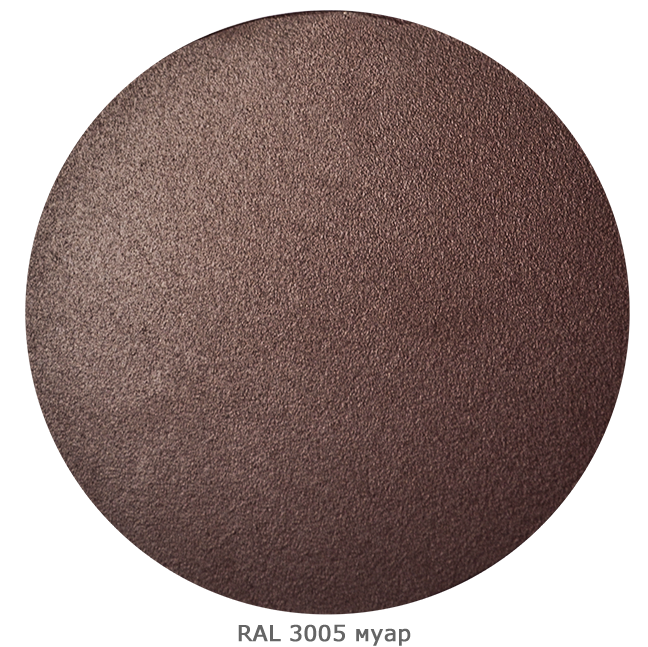
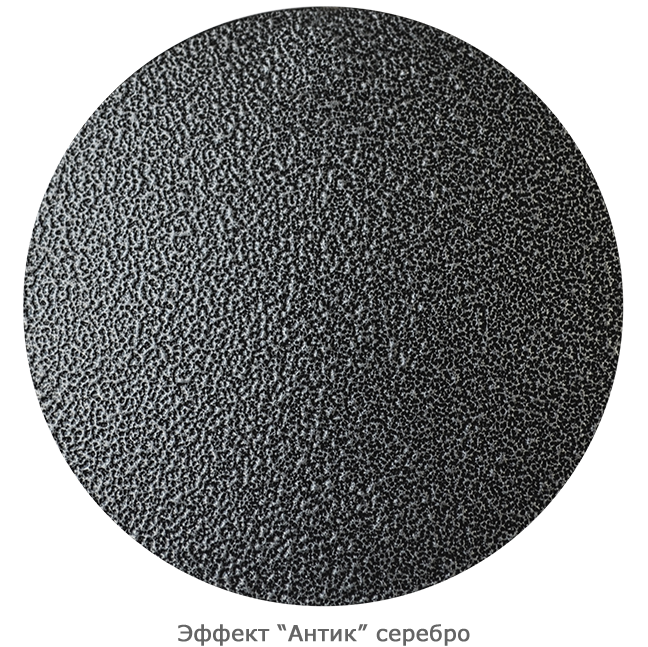
Рекомендованные толщины для полиэфирных,
эпокси-полиэфирных и полиуретановых порошково-полимерных красок и лаков AMIKA:
Тип формируемой поверхности |
Рекомендуемая толщина покрытия, мкм |
гладкая |
60 - 80 |
муар |
60 - 110 |
шагрень |
60 - 120 |
эффект «антик» |
80 - 200 |
эффекты «шелк», «кожа» |
60 - 180 |
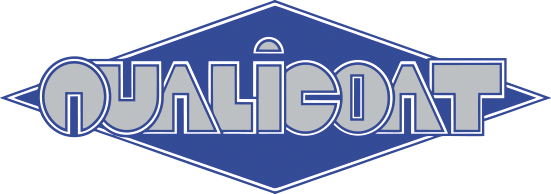
Архитектурные порошково-полимерные покрытия для алюминия Qualicoat должны соответствовать актуальной спецификации и заявленным в ней требованиям к толщине покрытия:
Класс 1 |
60 мкм |
Класс 1.5 |
60 мкм |
Класс 2 |
60 мкм |
Класс 3 |
50 мкм |
Двухслойное порошковое покрытие |
110 мкм |
Двухслойное порошковое покрытие PVDF |
80 мкм |
3. Цвет подложки и укрывистость краски.
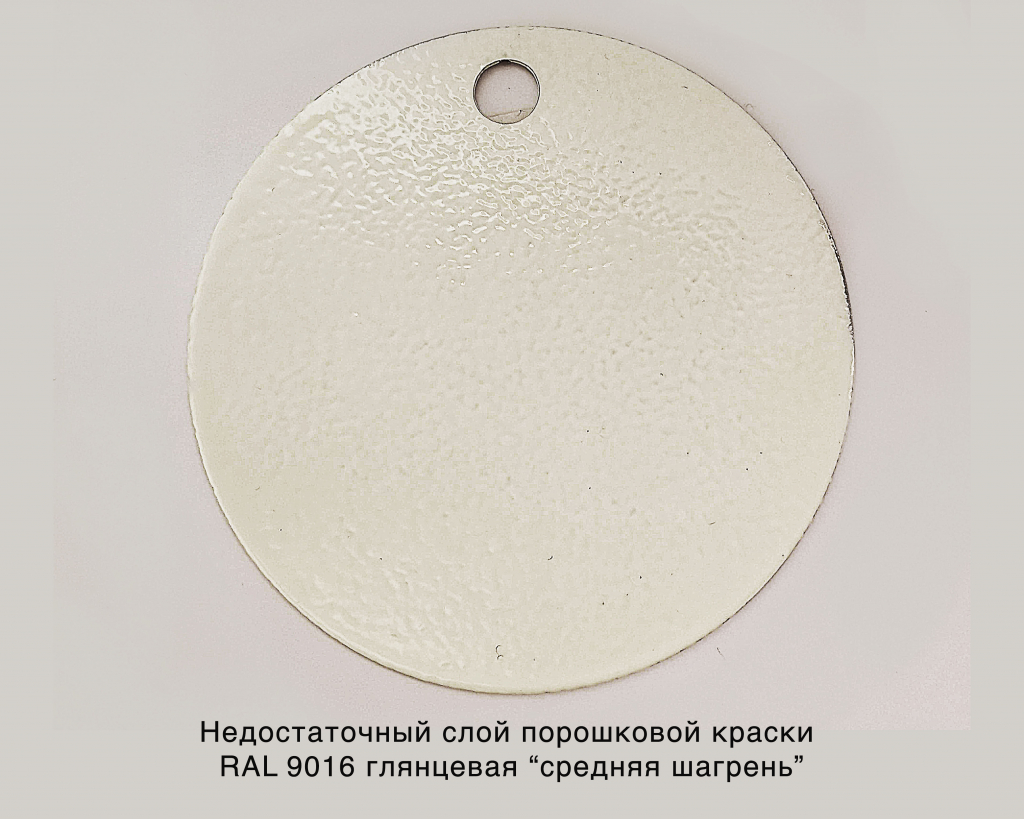
Чем больше контрастность между цветом металла и цветом лакокрасочного материала - тем меньше будет укрывистость лакокрасочного слоя.
Каждый цвет порошковых красок имеет разную способность укрывать подложку при одинаковой толщине краски. Белые, пастельные и желтые цвета порошковых красок, часто обладают меньшей укрывистостью. Следовательно, при большой контрастности субстрата и цвета краски, толщину слоя возможно придется увеличить.
4. Гранулометрический состав порошковой краски.
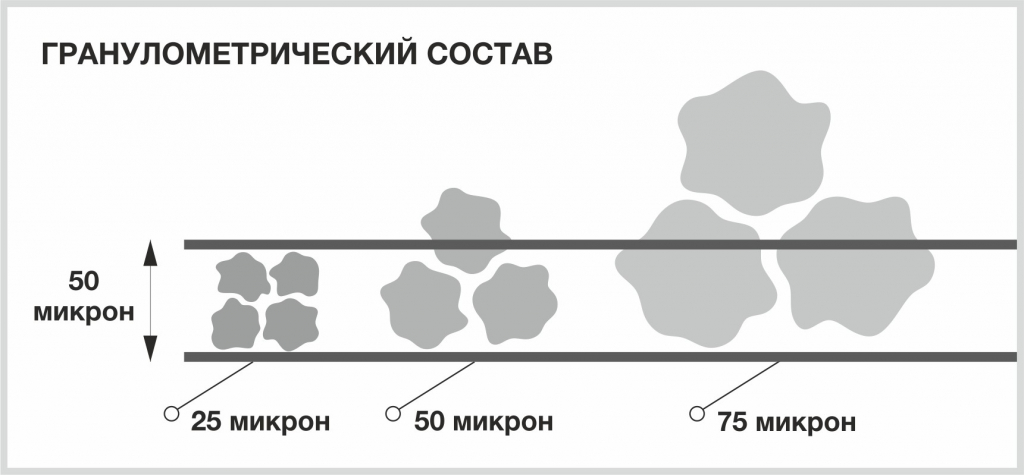
Гранулометрический состав характеризует размер частиц порошковых красок.
Тонкодисперсная краска (размер частиц от 10 до 50 мкм ) обладает меньшей сыпучестью, повышенной гигроскопичностью и требует тщательной настройки параметров оборудования. Толщина тонкодисперсной краски после отверждение не превышает 60 мкм. В основном, применяется для создания декоративных и тонкопленочных покрытий для бытовой техники.
Крупнодисперсный порошок (размер частиц от 110 мкм) обладает хорошей сыпучестью, но из-за большого размера частиц сложнее переносит заряд и образует гладкие покрытия с дефектом “апельсиновая корка”. Поэтому крупнодисперсную порошковую краску применяют для получения крупных текстурных покрытий муар и шагрень. Крупнодисперсные покрытия образуют толщину от 110 мкм и выше.
5. Метод нанесения и настройки оборудования.
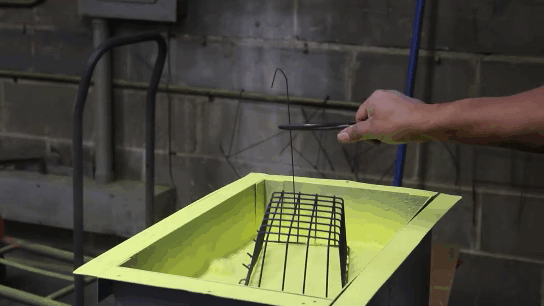
Покрытия, нанесенные методом окунания в псевдоожиженный слой, в среднем имеют толщину от 250 до 500 мм. При многократном нагревании и погружении толщина может достигать 2,5 мм, т.е. 2500 мкм.
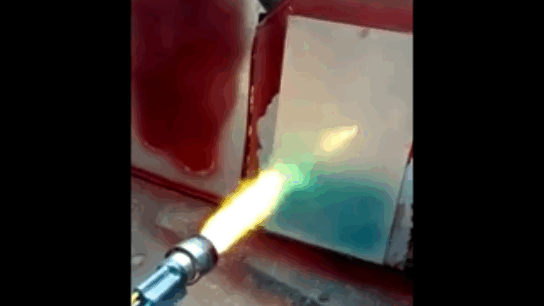
При газопламенном нанесении толщина варьируется от 200 до 600 мкм, при необходимости может достигаться и большая толщина пленки. Покрытия, полученные методом газопламенного напыления, не всегда имеют ровную поверхность, их назначение скорее имеет защитный, чем декоративный характер.
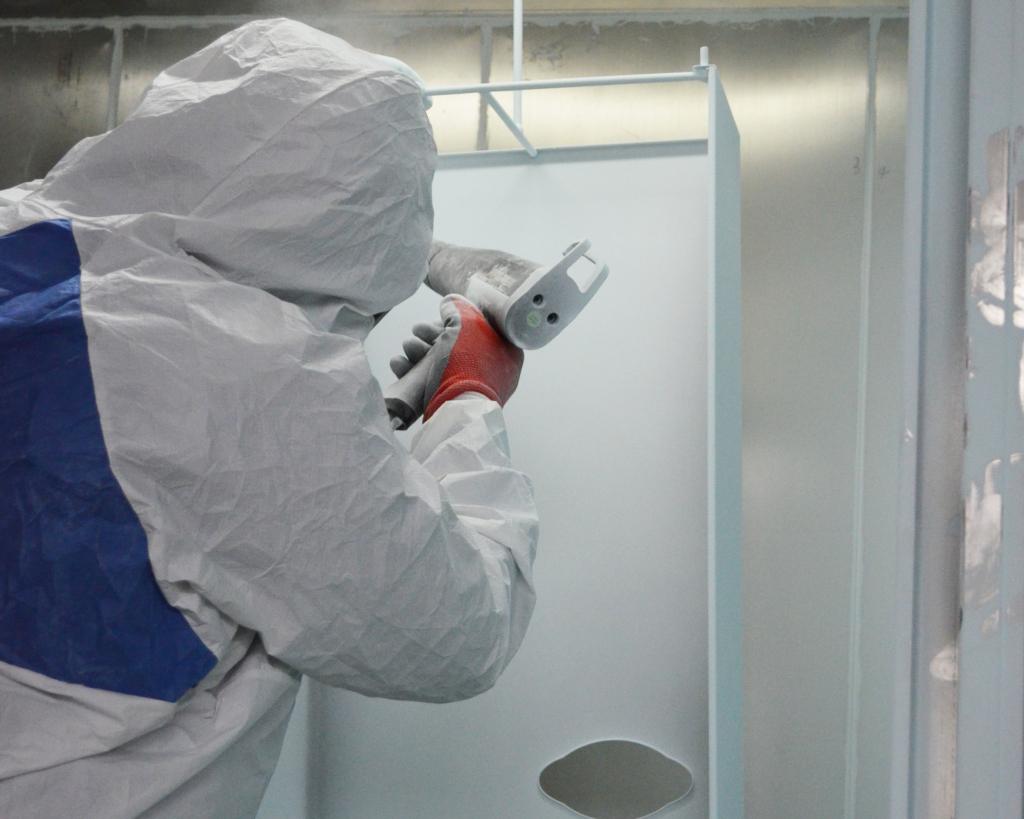
- концентрации порошковой краски в факеле распылителя;
- размера факела;
- скорости движения факела или времени прохода изделия через факел распылителя;
- напряжения на коронирующем электроде (степени зарядки порошковой краски);
- заземления изделия.
6. Форма изделия.
Из-за эффекта клетки Фарадея края изделия притягивают больше частиц порошка чем углубления. Чем сложнее форма изделия, тем больше вероятность того, что толщина порошково-полимерного слоя будет меняться по всей его поверхности.
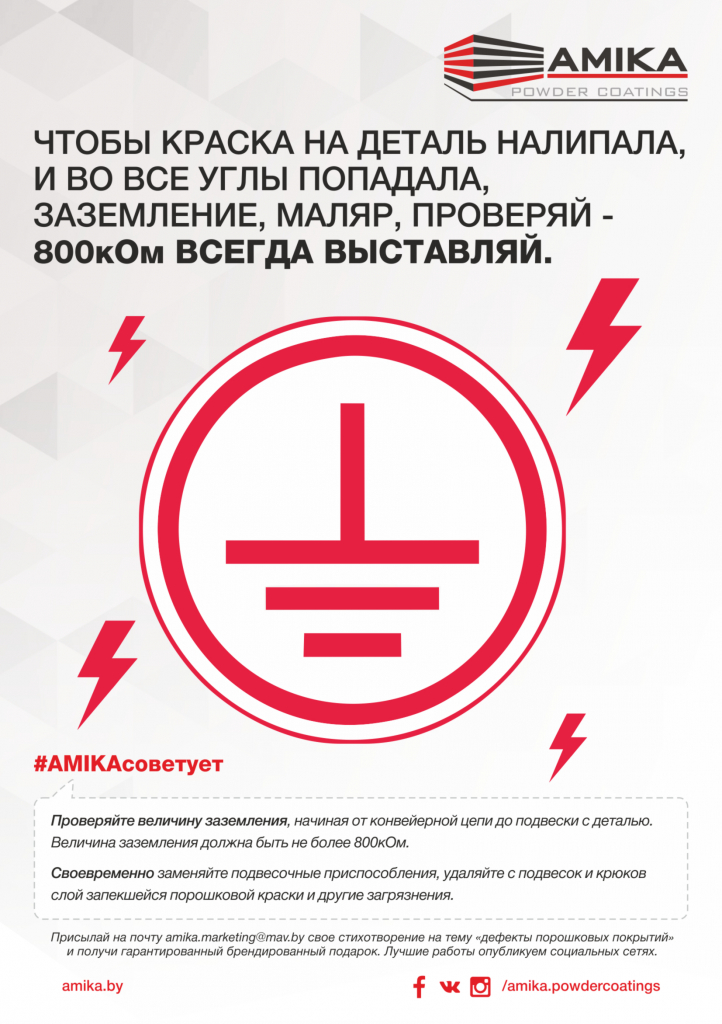
- Проверить напряжение на коронирующем заряде. Оптимальное значение 20 мкА;
- Проверить величину заземления, начиная от конвейерной цепи до подвески с деталью. Следите,чтобы величина заземления была не более 800 кОм.
- Уменьшить подачу порошка;
- Увеличить поток воздуха;
- Установить распылительные форсунки с формой, которая удлиняет факел распыления;
- Ежедневно очищать детали пистолета от слоя налипшей порошковой краски и вовремя заменяйте изношенные детали пистолета.
- Отрегулировать положение пистолета так, чтобы облако краски было направлено непосредственно в углубление.
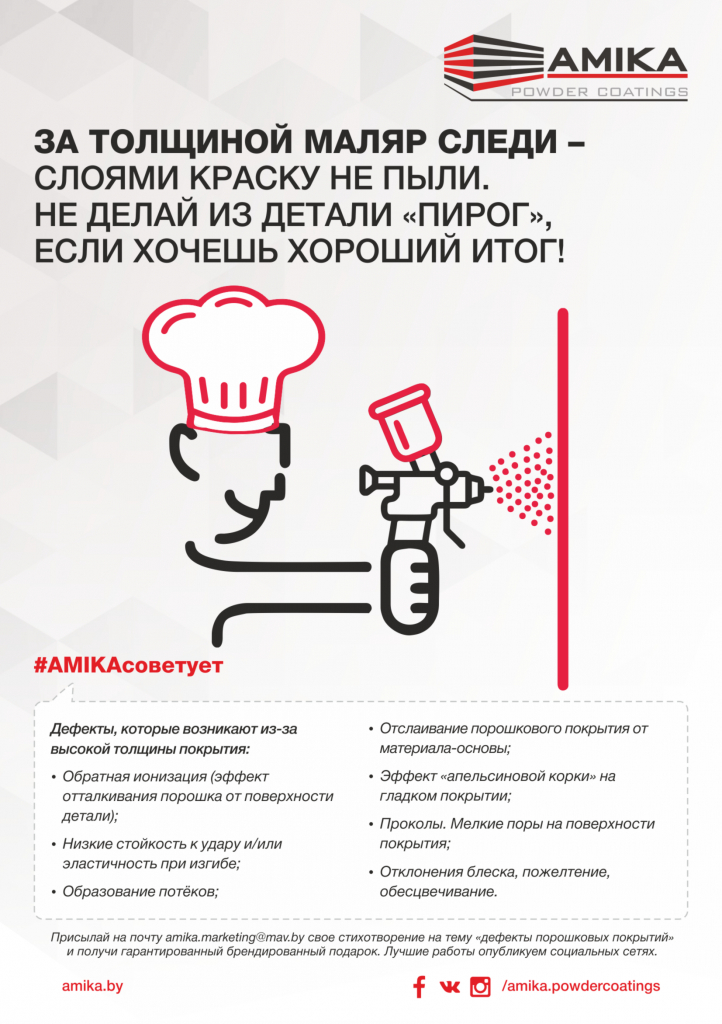
7. Человеческий фактор при ручном напылении.
Современное оборудование для нанесения порошковых покрытий сводит к минимуму человеческий фактор, однако полностью его исключить, особенно при ручном нанесении, невозможно.
Толщина порошкового покрытия при ручном напылении во многом зависит от внимательности оператора нанесения порошковых материалов и количества совершаемых им проходов .
Высокая квалификация оператора может обеспечить снижение расхода краски до 10 - 15%.
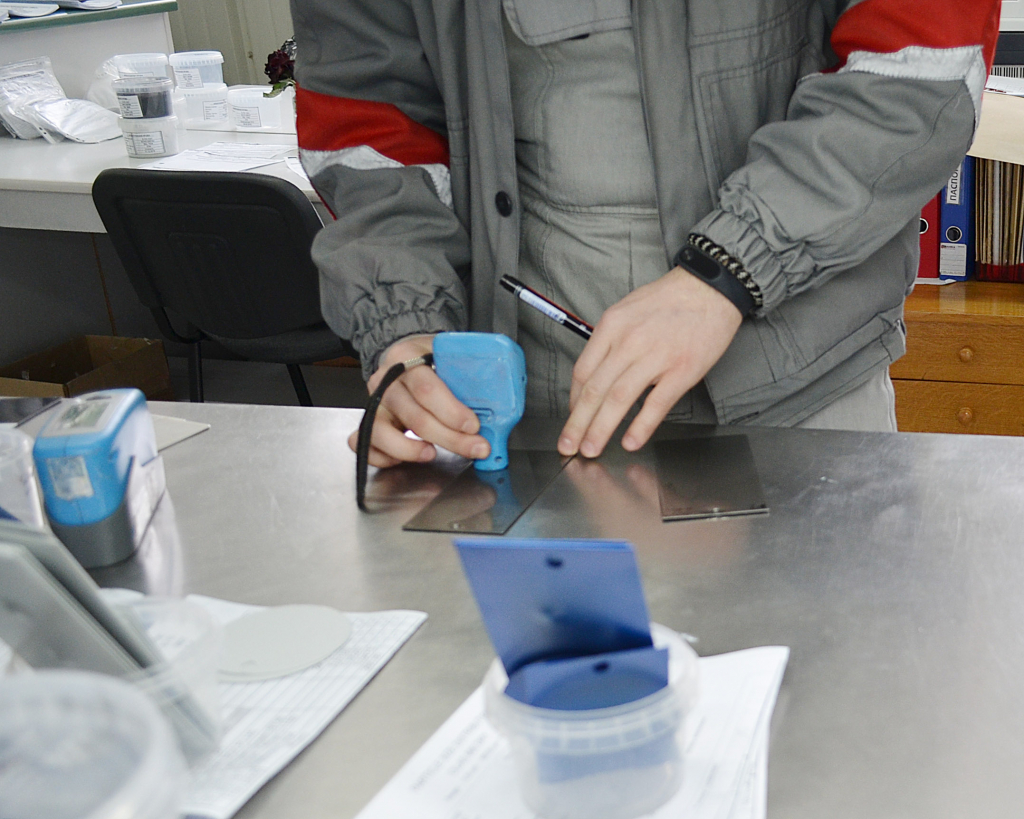
Как измерять толщину полимерного покрытия.
Для контроля толщины сформированного порошково-полимерного покрытия согласно ГОСТ 31993-2013 (ISO 2808:2007) чаще всего применяют толщиномеры, основанные на магнитном и вихретоковом действиях.
Данный толщиномер сочетает в себе оба вышеуказанных метода измерения. Для измерения на стали прибор использует магнитный метод, а для измерения толщины порошково-полимерного покрытия на алюминии - метод вихревых токов.
Толщиномер позволяет быстро определять толщину полимерного слоя на разных участках изделия и при необходимости корректировать процесс нанесения покрытий.
- Недостаточный и чрезмерный слой порошково-полимерного покрытия ведет к появлению дефектов полимеризации, снижает адгезию и физико-механические свойства покрытия.
- Толщина и равномерность полимерного покрытия зависит от назначения и типа формируемой поверхности; цвета подложки и укрывистости краски; гранулометрического состава выбранного материала; метода нанесения и настроек оборудования; формы изделия и квалификации оператора нанесения порошковых красок.
- Соблюдение рекомендованных производителем толщины и режима полимеризации покрытия гарантирует соответствие заявленным в технической документации физико-механическим свойствам.
- Внимательность и высокая квалификация операторов нанесения порошковых красок ожет обеспечить снижение расхода краски до 10 - 15%.
- Для контроля сформированного порошково-полимерного слоя руководствуйтесь ГОСТ 31993-2013 (ISO 2808:2007).
- Толщиномеры, основанные на магнитном и вихретоковом действиях, позволяют быстро определять толщину полимерного слоя на разных участках изделия и при необходимости корректировать процесс нанесения покрытий.
НОВОСТЕЙ