- 6 октября 2021
- AMIKA советует
Сотрудники отдела продаж и тех.сопровождения AMIKA - это та та «скорая помощь», которая всегда готова помочь Потребителям порошковых красок определиться с материалом, найти причину дефекта и просто узнать как дела.
На семинарах, интенсивах, вебинарах специалисты делятся своими знаниями и опытом, отвечают вопросы слушаетелей.
Для читателей блога мы составили топ-5 часто задаваемых вопросов технической поддержке AMIKA и ответили на них в 1 статье:
2. Зачем следить за температурой и влажностью воздуха на окрасочном участке?
3. Для чего контролировать качество сжатого воздуха и как это делать?
4. Почему забивается система подачи порошка?
5. Как плохое заземление влияет на качество порошкового покрытия?
1. КАК ДОЛГО ПРОСЛУЖИТ ПОЛИМЕРНО-ПОРОШКОВОЕ ПОКРЫТИЕ?
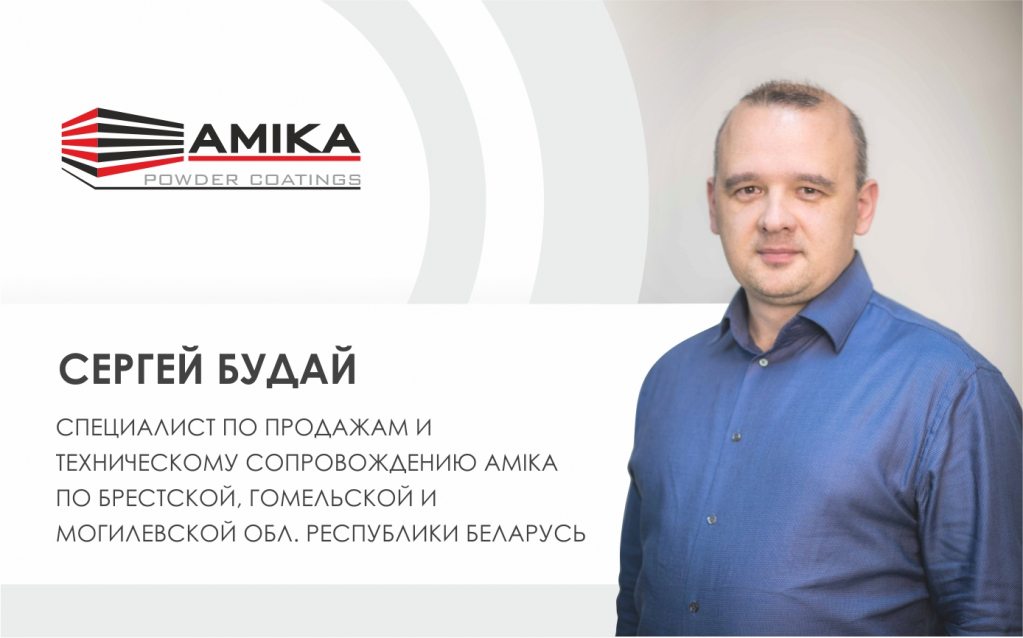
![]() |
Предварительной подготовки |
![]() |
Правильного выбора краски |
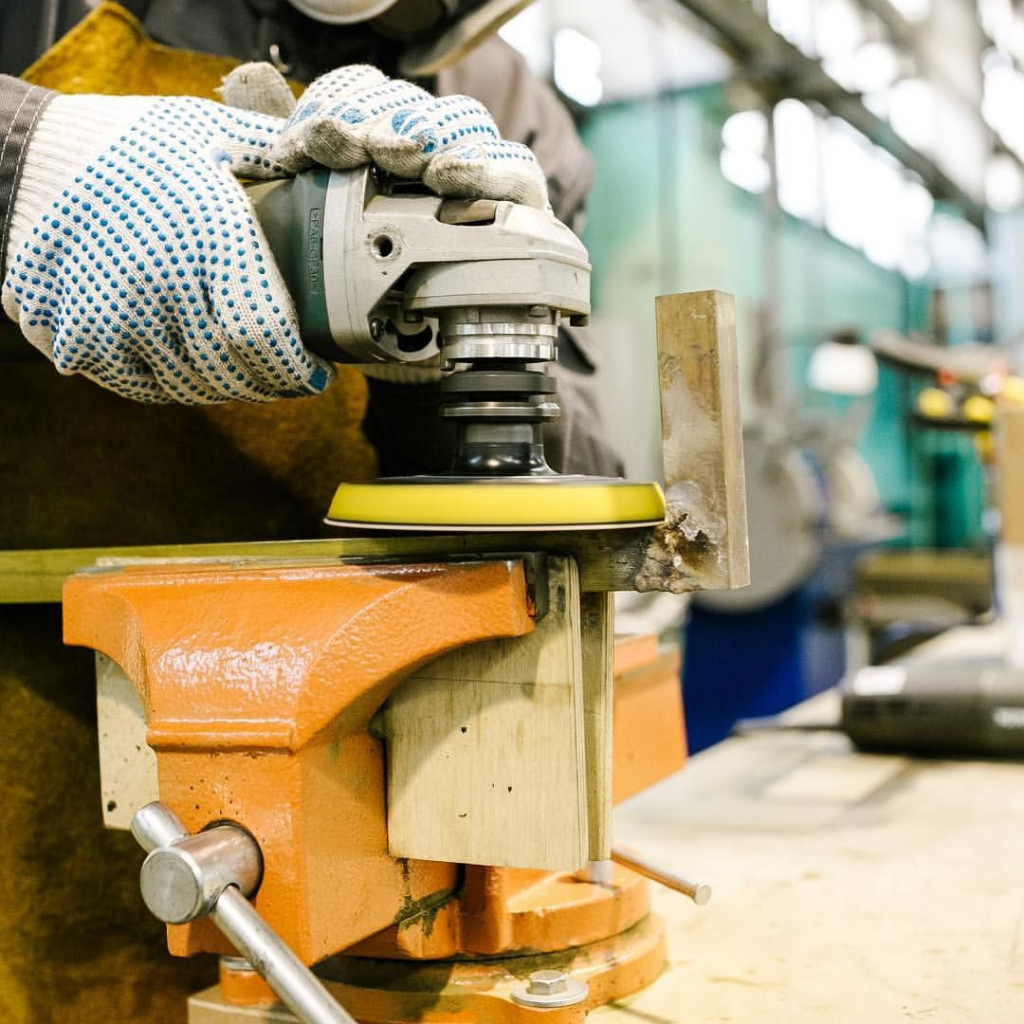
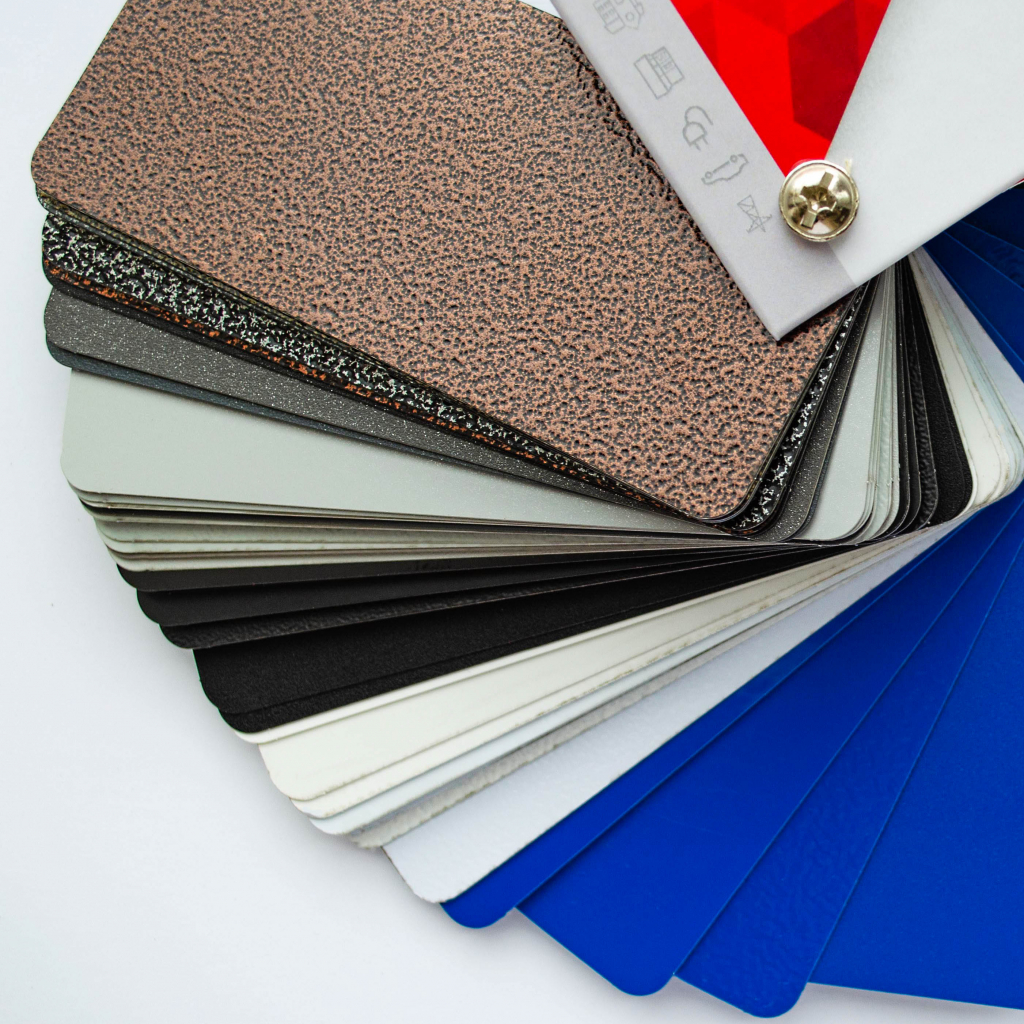
Первый и ключевой шаг в обеспечении максимального срока службы порошкового покрытия – тщательная предварительная очистка и подготовка изделия перед окраской.
Процесс предварительной подготовки включает в себя удаление существующей коррозии и очистку металла от загрязнений.
- твёрдые оксиды;
- солевые образования (окалина, ржавчина);
- продукты взаимодействия металла с окружающей средой;
- масляные и жировые плёнки, наносимые для облегчения обработки металлов;
- твёрдые и жидкие загрязнения, осаждаемые из воздуха промышленных помещений (пыль, металлические загрязнения, масла, силиконы)
Удаление загрязнений, коррозии, обезжиривание и химическая обработка обеспечивают хорошую адгезию порошковой краски с металлической подложкой, тем самым продлевают срок службы полимерного покрытия.
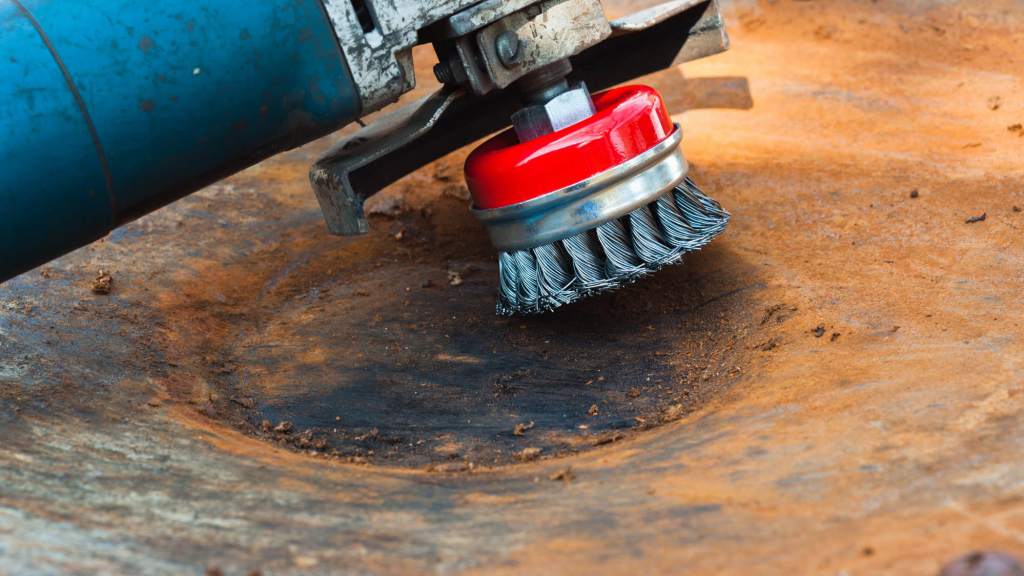
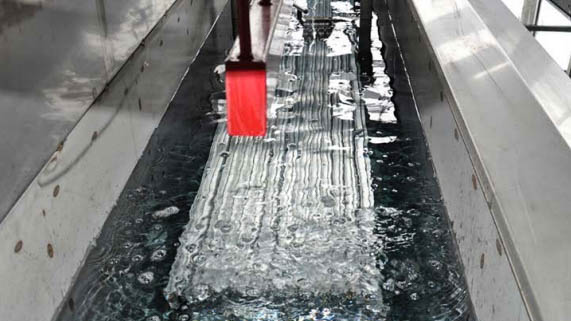
Правильный выбор лакокрасочного материала – следующий фактор, который влияет на срок службы порошкового покрытия.
По данным на сентябрь 2021 г., ассортимент порошково-полимерных покрытий AMIKA™ насчитывает 2989+ наименований.
Чтобы порошковая краска на 100 % соответствовала требованиям Потребителя и условиям эксплуатации окрашиваемого изделия, необходимо знать:
- в каких условиях будет эксплуатироваться окрашенное изделие;
- цвет, тип поверхности и степень блеска финишного полимерного покрытия;
- каким методом наносят порошковую краску;
- специальные требования к порошково-полимерному покрытию.
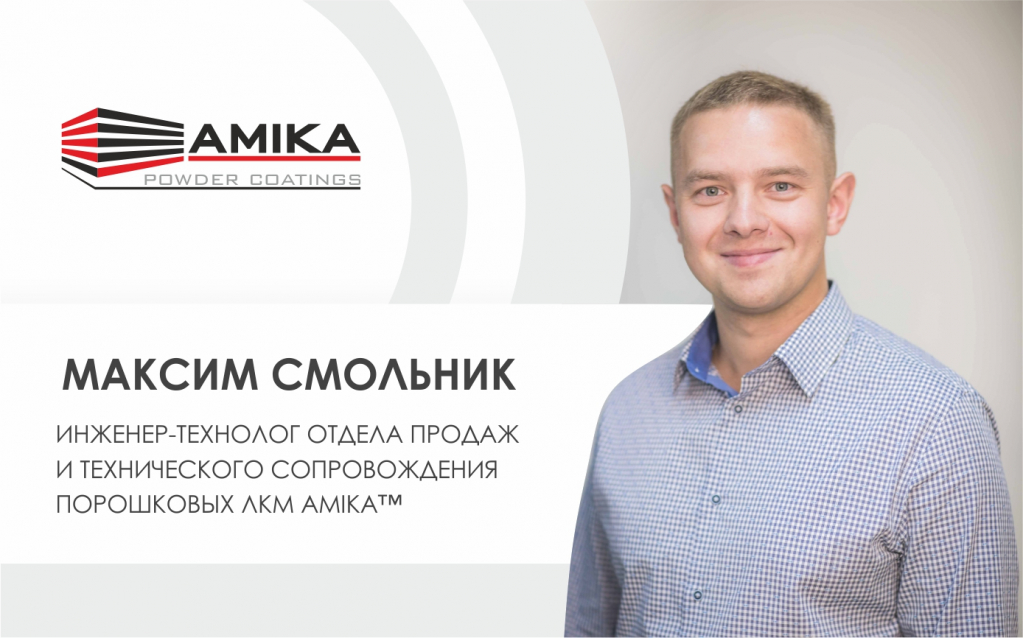
Нарушение температурного режима и уровня влажности воздуха на окрасочном участке негативно влияют на процесс электростатического напыления.
![]() |
Оптимальная температура воздуха на окрасочном участке - 15 - 30 °C |
![]() |
Уровень относительной влажности воздуха - не выше 80% |
При высокой влажности воздуха, ухудшается заряжаемость частиц порошковой краски, что приводит к:
- снижению эффективности окрашивания;
- увеличению расхода порошкового материала;
- большому количеству рекуперата.
Проверить влажность воздуха на участке можно с помощью специального прибора – психрометра. Принцип его действия прост: вы снимаете показания с двух термометров, один из которых находится во влажной среде (смоченная губка или ткань), а второй остается сухим.
Сопоставив показания двух термометров со специальной таблицей определяем относительную влажность воздуха, климатические условия на участке окрашивания и делаем выводы о готовности участка к покраске.
Психрометр |
Таблица психрометра |
![]() |
![]() |
не открывайте коробки с краской сразу после получения.
Поместите их в закрытом состоянии возле линии окрашивания минимум на 24 часа,
а лучше на все 48.

Сжатый воздух – это определяющий фактор аэродинамической картины нанесения порошка.
- переводит порошок во взвешенное состояние;
- создает отрицательное давления внутри эжекторного насоса;
- поддерживает необходимую скорость воздушно порошковой смеси.
При сжатии воздуха любой водяной пар, а также загрязняющие вещества, имеющиеся в нем,
существенно увеличиваются.
Влага, грязь и масла при подаче воздуха оставляют дефекты поверхности, затрудняют порошковый поток и причиняют вред распыляющему оборудованию.
Поэтому необходимо проводить подготовку сжатого воздуха, которая заключается в пропускании его через каскад пылемаслоулавливателей и аппарат воздухосушки.
Экспресс-метод определения качества сжатого воздуха
Мы рекомендуем проводить такие мероприятия перед началом каждой смены, после ремонтов,
а также после появления дефектов покрытия.
И вот вы учли все факторы, убедились в качестве сжатого воздуха, температуре и влажности на участке,
а система подачи порошка забивается и краска подается неравномерно, возникает новый вопрос …
Оплавление порошковой краски в шлангах – одна из причин неравномерной подачи материалов.
Это явление получило название «ударная полимеризация» или «ударное сплавление».
Ударная полимеризация
Почему на внутренних стенках окрасочного оборудования образуются наросты полимерной краски?
При слишком высокой скорости воздуха, порошковая краска нагревается и начинает сплавляться с другими частицами, постепенно образуя скопления порошка на изгибах транспортировочных шлангов.
- препятствуют эффективной подаче порошка;
- мелкие образования являются причиной «сорности» полимерного покрытия;
- более крупные агломераты приводят к прерывистой подаче материала, образуя так называемые «плевки».
Любая часть оборудования для нанесения порошка является потенциальной зоной для ударного сплавления.
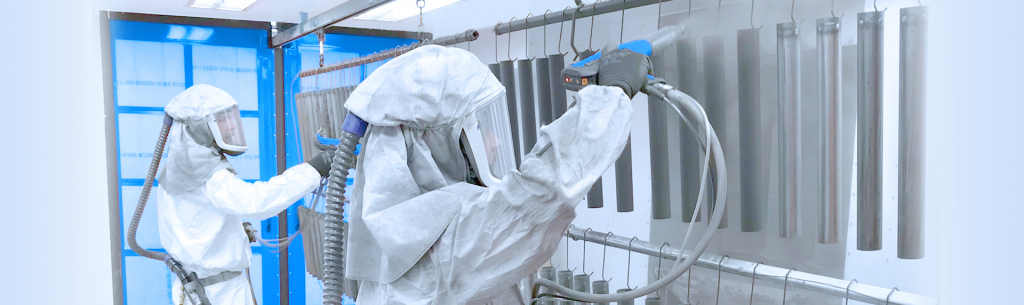
- избыточное давление воздуха и скорость в системе подачи порошка;
Рекомендуемое давление воздуха на входе в распылитель – 0,1 – 0,6 МПА (1-6 Бар).
- высокая температура на окрасочном участке;
- наличие изгибов, изломов и пережатий шлангов;
Минимально допустимый радиус закругления шланга - 220 мм.
- загрязнение и износ окрасочного оборудования;
Вовремя заменяйте и очищайте трубки, шланги, насосы и форсунки.
- Избыточное количество рекуперата в порошковом материале.
Максимально допустимое соотношение рекуперата к свежей порошковой краске 30:70.
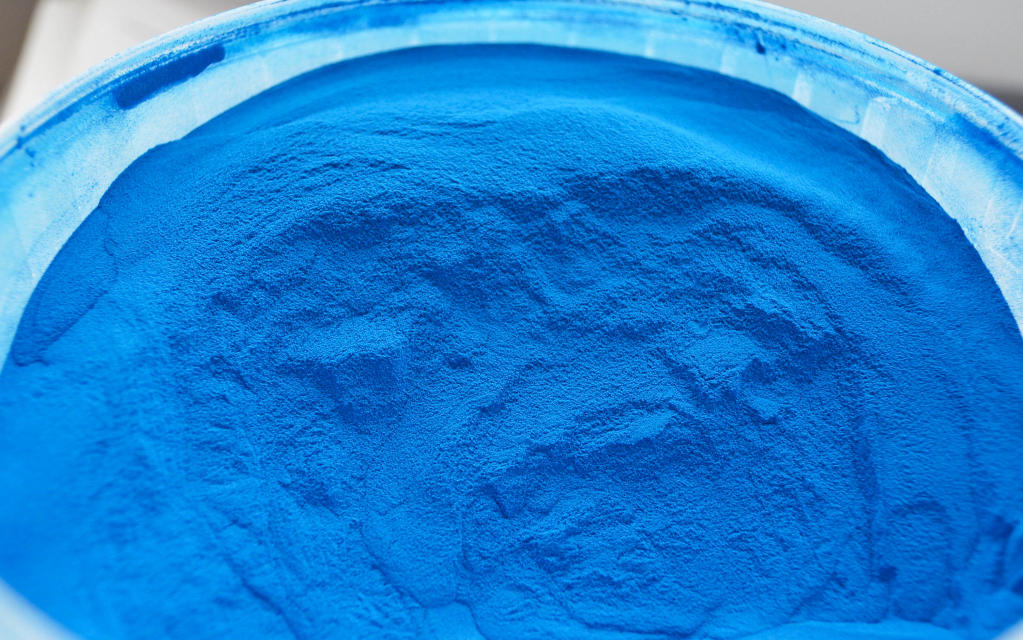
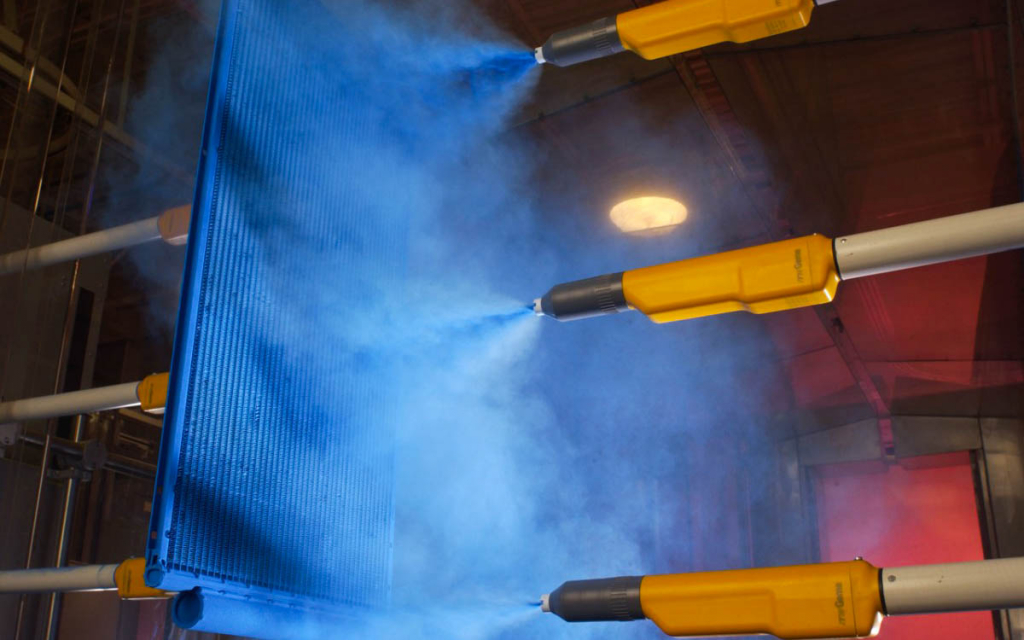
В первую очередь, заземление – это защита человека и оборудования для порошковой покраски от поражения электрическим током.
Движущийся в распылителях порошковый материал является источником статического электричества.
Качественное заземление гарантирует как безопасность на производстве, так и является основополагающим условием осаждения материала на деталях - благодаря заземлению порошок удерживается на изделии и не осыпается.
- порошок плохо осаждается и отталкивается от поверхности детали - эффект обратной ионизации ;
- частицы порошковой краски не проникают в отверстия и углы - эффект Фарадея;
- избыточный статический заряд - порошковая краска налипает на поверхность окрасочного оборудования.
- проверить величину заземления, начиная от конвейерной цепи до подвески с деталью;
Важно знать!Сопротивление заземлению должно составлять не более 1 МОм.
800 кОм- 1МОм – допустимым
>1 МОм – плохим и не допустимым. - своевременно производить замену подвесочных приспособлений, удалять с подвесок и крюков слой запекшейся порошковой краски;
Запекшаяся порошковая краска выступает в этом случае как диэлектрик и препятствует стеканию электрического заряда с изделия.
- Применять токопроводящую смазку для роликов конвейера.
- На срок службы порошково-полимерного покрытия влияет тщательная подготовка поверхности перед окраской и правильный выбор порошковой краски.
- Нарушение температурного режима и уровня влажности воздуха на окрасочном участке негативно влияют на заряжаемость порошковой краски.
- Чистый сжатый воздух предотвращает появление дефектов внешнего вида полимерного покрытия. Проверку качества сжатого воздуха можно проверить путём обдува чистого зеркала в течении 3-х минут. Отсутствие запотевания или следов свидетельствует о хорошем качестве сжатого воздуха.
- При слишком высокой скорости воздуха, порошковая краска нагревается. Как следствие, частицы порошка сплавляются и скапливаются на изгибах транспортировочных шлангов и внутри окрасочного оборудования.
- Качественное заземление гарантирует безопасность на производстве и является основным условием осаждения порошка на детали - благодаря заземлению частицы удерживаются на изделии и не осыпаются.
Возник дефект откуда не ждали?
Техническая поддержка AMIKA поможет разобраться с причиной и найти решение!
Расскажите о своей проблеме, а мы поможем!
НОВОСТЕЙ